●千代田化工建設の大河会長は、2020年年頭メッセージで、仕事への向き合い方として、「『自らが考える思考型』の取り組みスタイルへの意識転換」と、「『働き方改革』への取り組み」の二点を挙げられました。
●「自らが考える思考型」では、「目の前の課題や問題に『なぜか?』を繰り返し、自分自身でその意味するところの背景や本質を十分理解し、新たな価値を生み出して頂きたい」としています。
●考えが深いとは、トラブルが起こったような時に、眼前の事だけに目を向けるのではなく、その原因やさらに原因の原因など、背後に隠れている事象にまで考えを及ぼせることでしょう。●では、どうすれば物事を深く考える事が出来るようになるのでしょうか。
原因を探る方法
●どの様な事でも、その原因となっているものがあります。●例えば、「朝、起きられない」という事象には、病気や怠惰、目覚ましの故障などの表面的な原因が考えられますが、もっと深く考えてみると、ゲームをしていて就寝時間が遅かったり、ホラー映画で興奮して眠れなかったり、仕事の悩みだったり・・・・、様々な原因が浮かんできます。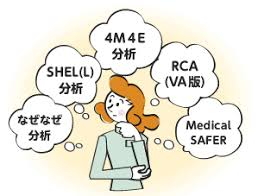
●物事の本質を探る方法としては、問題をツリー状に分解してロジカルに原因や問題解決策を探す「ロジックツリー」、なぜ?ほんとう?それから?を視覚化する「UDEツリー(Undesirable Effect)」、良いことと悪いことの一覧表する「プロコン・リスト」、解決策毎にシミュレーションする「ディシジョンツリー」、問題の芽を見つけるために役に立つ「ダウンサイドリスク(最悪の状態につながったときに被る最大限の損害)」、四つのプロセス(問題を明確化する、原因を考える、解決策を立案する、実行する)で問題を解決する「ロジカルシンキング」など様々な考え方があります。
●中でも一般的に知られているのは、「なぜなぜ分析」、「4M5E分析」、「特性要因図(フィッシュボーンチャート)」です。●「なぜなぜ分析(5why分析)」は、自動車メーカーのトヨタが取り入れていることでも有名で、ミスが生じた原因をさらに深掘りして根本的な原因を探る手法です。●「4M5E分析」は、4つの原因(4M)と5つの対策(5E)に分類して、多角的な視点で解決策を探る手法です。●「特性要因図(フィッシュボーンチャート)」は、もともとは製造業で起こり得る問題の原因を特定し、有効な対策を講じるための手法として広く用いられ、潜在的な問題を見つけるための手法として広く応用されるようになりました。
なぜなぜ分析「5why」
■なぜなぜ分析とは、もともと生産の現場でミスの再発防止や、品質向上のために用いられる分析方法で、問題の根本的な原因を探るために、問題が起こった理由が「なぜ発生したのか?」を繰り返し質問することで、真の原因を究明する分析方法です。■なぜなぜ分析はトヨタ自動車の元副社長だった大野耐一氏の著書「トヨタ式生産方式」によって、広く知られるようになりました。
■「なぜ?」を繰り返さない場合は、表面的な思考・行動に陥りがちです。または、問題が起こる要因を、本当の原因であると勘違いしてしまいます。要因はあくまでも、1つの可能性であって、事実ではありません。ファクトベースの思考こそが、真の原因にたどり着くことができます。■例えば、「生産台数を、期日に仕上げることができない。何とかならないか?」と会社から求められたとき、「なぜ?」が抜けている人は、「残業してでも頑張ります」「スタッフを増やして対応します」となります。ここで「なぜ期日に間に合わないのか?」と問いかけることが、「5why」のスタートラインです。
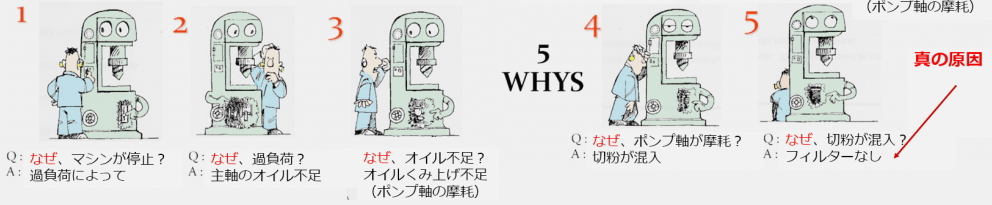
■大野氏は著書の中で、「一つの事象に対して、五回の「なぜ」をぶつけてみたことがあるだろうか。言うはやさしいが、行うはむずかしいことである。五回の「なぜ」を自問自答することによって、ものごとの因果関係とか、その裏にひそむ本当の原因を突き止めることはできる」■「トヨタ生産方式」では、例題として「機械が動かなくなった場合」の分析が紹介されています。
■【課題】機械が動かなくなった→【なぜ1】なぜ機械は止まったのか?(オーバーロードがかかって、ヒューズが切れたから)→【なぜ2】なぜオーバーロードがかかったのか?(軸受部の潤滑が十分でないから)→【なぜ3】なぜ十分に潤滑しないのか?(潤滑ポンプが十分汲上げていないから)→【なぜ4】なぜ十分汲上げていないのか?(ポンプの軸が摩耗してガタガタになっているから)→【なぜ5】なぜ摩耗したのか?(ストレーナー[濾過器]が付いていないので、切粉が入ったから) |
4M5E分析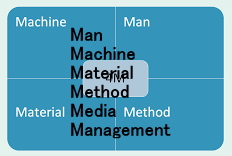
■4M5Eは主にヒューマンエラーに対しての分析方法として有効性があるとされています。エラー要因を多面的に捉えるとともに、対策も広い観点から検討できるとされています。起源はNTSB(米国国家運輸安全委員会)の事故調査手法が起源とされています。
■4M5Eの4Mは、Man(人間要因)、Machine(機器要因)、Media(情報要因)、Management(管理要因)、5EはEducation(教育・訓練)、Engineering(技術・工学)、Enforcement(指導・徹底)、Example(対策・規範)、Environment(作業環境)を指します。4M5E分析は、多様な原因について偏りなく分析しやすいことがメリットです。
Man(人間要因):危険な行為・手順/規律無視の行為・共同作業場の行為・職場の人間関係・不安全な姿勢
Machine(機器要因):取り扱い物・機械設備の欠陥・安全装置/保護具の欠陥・本質安全化の不足・点検整備の不足等
Media(情報要因):照明、騒音をはじめとする物理的環境、手順などの情報環境、同僚などの人間環境などの環境要素
Management(管理要因):管理組織の欠陥・作業手順の不備/不徹底・作業工程計画の不良・教育訓練の不足・指導/監督の不足・適正配置の不十分・健康管理の不良など
Education(教育・訓練):業務遂行のために必要な能力、意識向上のための対策。講習会、OJTの実施など。
Engineering(技術・工学):安全性を向上させるための機器・設備、方法の技術的な方策。設備や手順、基準値の見直し。
Enforcement(指導・徹底):業務を確実に実施するための強化・徹底に関する方策。手順の作成、危険予知活動の強化。
Example(事例・模範):不正やマニュアル外の作業を行わないような模範行動。社外事故事例の共有、情報のデータベース化など。
Environmnet(作業環境):物理的な作業環境を改善する方策。作業場の照度や騒音などの改善 |
特性要因図
■特性とは現在見えている結果のことを指し、要因とはその結果をもたらすのに影響を与えた要素のことです。特性要因図は、結果である特性がどのようにしてもたらされたかを図式化して、そこに潜んでいる問題点をあぶり出すのに用いられる手法のことです。■見えているもの、見えていないものそれぞれを含めて出し尽くすことから問題の本質を探る特性要因図には、「課題の洗い出し、解決から先入観を排除できる」、「問題解決の方法論や品質が安定する」、「ノウハウとして蓄積され、情報資産となる」、「視覚化されるため問題意識を共有しやすい」などのメリットがあります。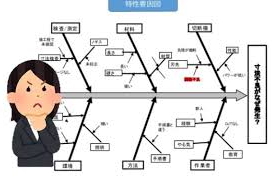
■特性要因図の歴史は古く、1953 年に東京大学の教授を務めていた石川肇氏が考案したのが始まりとされています。実際の特性要因図を見ると分かるのですが、魚の骨にとてもよく似た形をしているため、フィッシュボーン(魚の骨)図、フィッシュボーンチャートなどと呼ばれることもあります。特性に対する原因究明に困ったら図に書き出してみるのが一番ですが、その時に活躍するのが特性要因図です。
■実際に図式化された特性要因図を見ると、魚の骨を構成する 4 つの要素が見て取れます。これらは魚の骨になぞらえて、背骨、大骨、小骨などと呼ばれています。■背骨は解決したいテーマ、大骨はすぐに思いつく要因、小骨は大骨の問題を生み出している個々の要素、孫骨は小骨の原因をミクロの視点で考察したもの。■特性要因図の要因をあぶり出す際に意識されるのが、4Mと呼ばれる要素です。すべてMから始まる英単語の、Man=人、Machine=機械・設備、Method=方法、Material=材料、で表現されます。
|